The Nursery Sod Growers Association (NSGA) of Ontario held a 2-hour side-by-side field demonstration of harvesters from three manufacturers. The FireFly R300 outperformed the other machines across all measures.
Hats off to Peter Rauwerda from Greenhorizons Sod Farms (Cambridge) and the NSGA of Ontario for putting together such an equitable way for their members to evaluate the productivity of mini-roll harvesters from different companies.
The FireFly R300 harvester went head-to-head with a Brouwer 4000 and a Trebro AutoStack 3 (a double-head harvester) in identical fields of beautiful Kentucky bluegrass, with favorable conditions for harvesting.
Here are the results.
It was a clean sweep for the FireFly machine, getting the most grass out of the field in both sections with less waste, and at the fastest speeds.
Get a Quote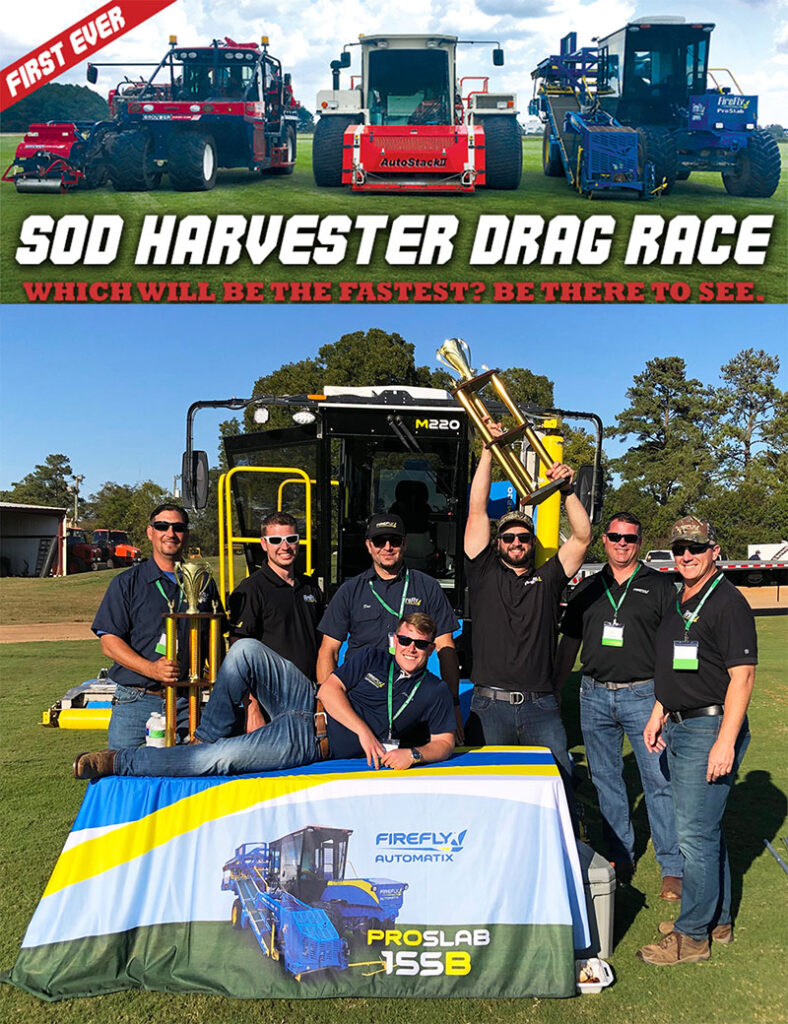
The FireFly team welcomes any challenge, as was seen at the 2019 Sod Harvester Drag Race in Georgia, where FireFly harvesters took first place in both the Roll and Slab races.
The R300 cleaned up in the Clean Up Area.
Here’s how the contest worked.
Each machine started in a triangular “clean-up” area which would require more turns. The FireFly was the first to finish and had the highest yield and productivity. Factors that gave the R300 an advantage in this section include our cab’s clear sight line to the cutter head and FireFly’s exclusive ability to continue rolling and stacking during turns while the cutter head is lifted.
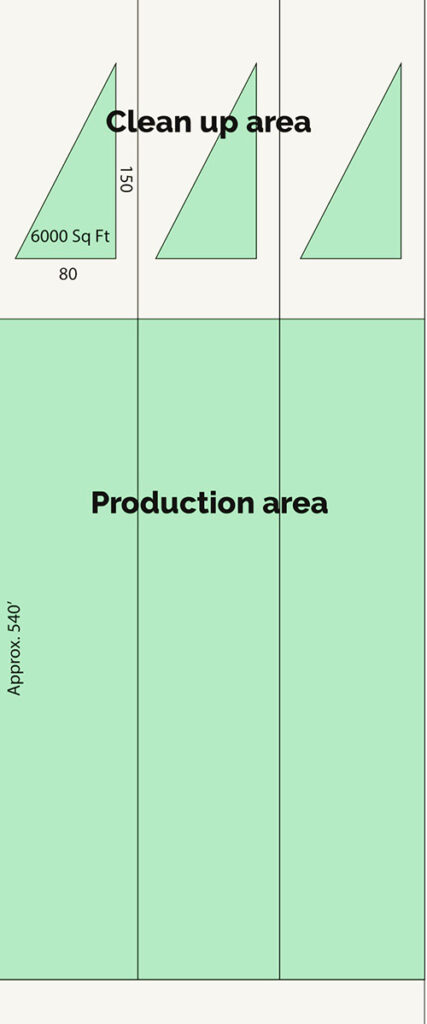
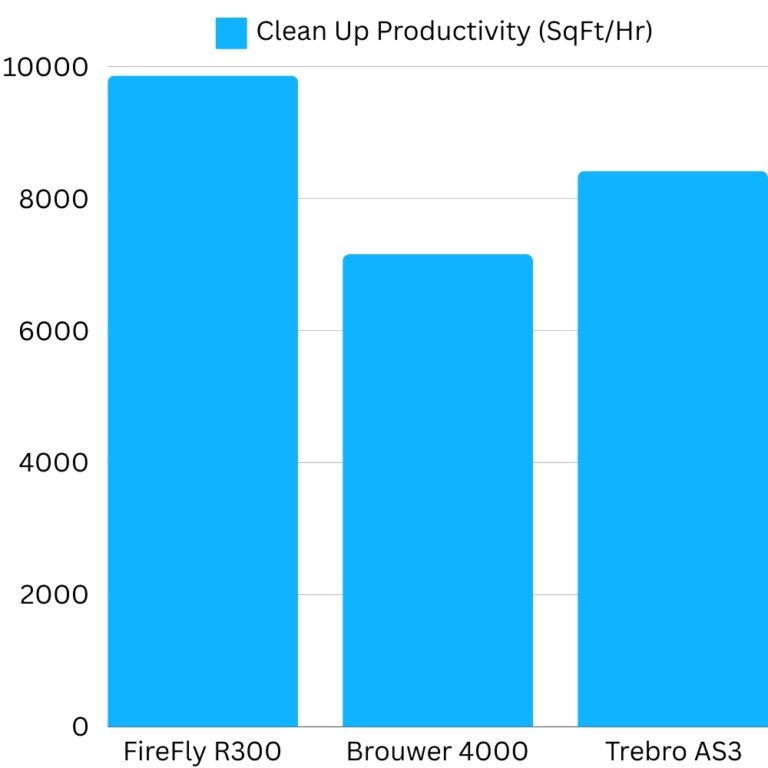
FireFly also had the highest productivity in the Production Area.
Once the harvesters finished their triangles, they moved into a rectangular “production” area. Unfortunately, the AutoStack had to stop after a few pallets due to a malfunction, but the competition continued between the FireFly and the Brouwer. FireFly’s productivity rate in this section was 23% higher than the Brouwer harvester.
At the end of the two hours, the FireFly R300 had cut 28,955 ft2 (2690 m2) with a 33% higher overall productivity rate than the Brouwer.
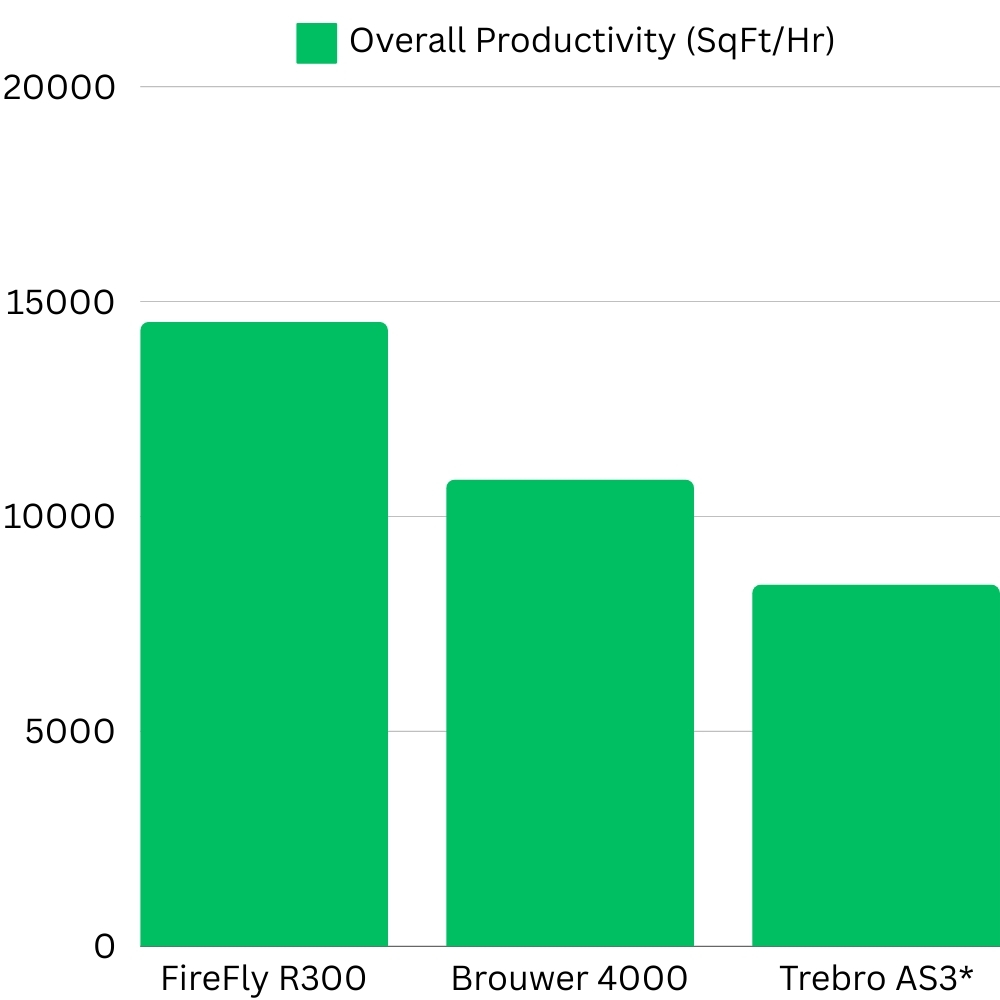
*Trebro’s productivity could only be measured in the Clean Up Area, due to a machine malfunction in the Production Area.
What’s behind FireFly’s higher overall productivity? Electric control.
The FireFly was moving at 1.9 to 2 mph. Operating at these speeds in such ideal conditions is normal operation for the R300, so it was no surprise that it was smooth sailing for our machine. And because our conveyors and roll-up are electrically controlled, movements are always precise, keeping flaps perfectly consistent even at high speeds.
In addition, our machine uses AI to intelligently adapt to any variations to ensure every flap is perfect (did you see those perfect pallets?). This all happens without any intervention from the operator.
But what about fuel economy?
We also decided to add our fuel economy to the numbers. The R300 only used 3.7 gallons (14 liters) of diesel in two hours. That means at even at these high speeds, the R300 had a fuel economy of 1.85 gal/hr (7 liters/hr) and fuel consumption per productivity of 1.28 gallons per 10,000 ft2 of grass cut (5.2 liters per 1000 m2).
We hope to see more events like this. It was a great opportunity to demonstrate the capabilities of the R300 that we see on a daily basis. If you want to know more about how FireFly technology can benefit your farm, let us know.
Get a quoteThanks again to Greenhorizons and the NSGA of Ontario!